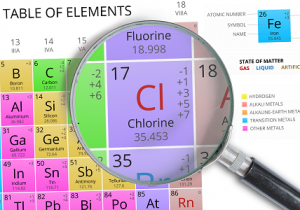
Chlorine (CL2) is a member of the halogen elements group that is highly reactive and bonds easily with hydrogen to form HCL acid. HCL attacks stainless steel aggressively - literally passivating the surface of the stainless steel, and can render a thermal mass flow controller inoperative in a brief period of time. CL2 is used frequently in many applications from making PVC pipe and treating water to plasma etching a computer chip. CL2 is a critical process element in our world. CL2 mass flow controllers typically have a significant life span reduction which can be improved using tightly managed process controls. So what needs to be controlled in a CL2 process?
1) Leak test your system
The primary contaminant component for CL2 applications is air and its entrained moisture (water) content. To avoid this process "invasion" it is imperative that the entire system be leak tight at the onset of work. The best (and cheapest) way to do this is to pressurize the line with clean, dry nitrogen (N2) to 50 PSIG. Make sure the line is not blocked in any way with shut off valves, etc. Measure the line pressure as accurately as possible and allow the piping to stand in a static mode for a 24 hour period or longer if possible. Recheck the pressure reading to verify no decay has taken place. It is best to verify leak integrity in a temperature stable environment.
2) Pump purging before every start up and after every process run
Eliminating air content in the process line before CL2 is introduced is essential to a successful startup procedure. Purging the process path after a process run will further enhance the longevity of your CL2 mass flow controllers. Cycle-purging using dry N2 is the best method to accomplish the purging process. This is accomplished by raising the N2 purge gas line pressure to 30 PSIG and then exhaust to a small backpressure of 1-3 PSIG. This backpressure will protect the process line from back flow of air. This process should be repeated at least 15 times to evacuate as much air or other moisture bearing gas from even the smallest dead space in the line. Maintaining a high vacuum state in the process line after this this cycle- purging is completed will qualify a "clean" system for CL2 service.
3) Eliminate the possibility of contamination from the N2 purge source
The N2 purge source should be certified to have less than one part per million (1 PPM) of moisture/O2 in it. This should be verified periodically with in situ testing. It is best to use a dedicated N2 purge gas line for CL2 services. Ideally, specialized gas purifiers (as used in the semiconductor industry) should be used just prior to the point of process gas use as a primary precautionary method. These purifiers are a necessity to achieve better than 100 parts per billion moisture content which is the recommended "safe" level to minimize / eliminate the production of hydrochloric acid in the process stream.
4) Use the appropriate/best mass flow controllers for CL2 service
The ideal thermal mass flow controller for CL2 gas service is the Brooks Instrument metal sealed GF80 Series or GF100 Series. Metal seals eliminate the possibility of outgassing thru elastomeric o-rings, keeping air out of the flow stream. These products have essential functional components made of Hastelloy C-22 - flow sensor, valve seat, and valve orifice. Hastelloy C-22 is inherently corrosion resistant to CL2. Additionally the GF80 Series and GF100 Series products have a 10µ inch Ra surface finish or better for particle free function. The exceptional performance of the GF series is enhanced by our MultiFlo™ technology - gas and range programmability embedded in the electronics of each device. Actual CL2 gas was used to establish an empirical CL2 gas calibration table inherent in every GF Series product. The GF80 and GF100 Series will exceed your expectations for the best accuracy and performance in your CL2 application!
Component datasource missing. Select a datasource for this component.